Smart Manufacturing Transformation Depends on Modern Workforce Management Capabilities
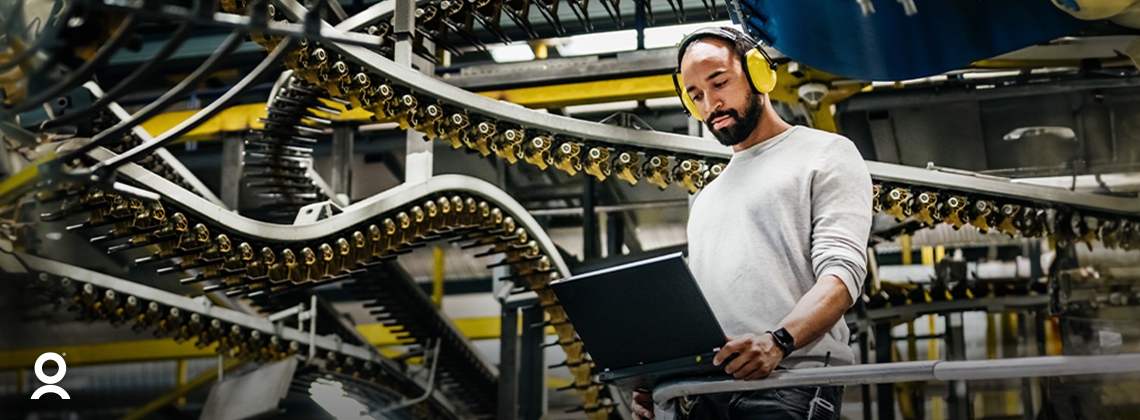
The manufacturing industry is at a crossroads as significant and rapid changes in market dynamics leave manufacturing organizations to face uncertain economic headwinds. These challenges are paired with a significant transformation in workforce demographics as the emergence of a younger workforce and a tight labor market calls for increasingly strategic approaches to attracting and retaining talent, as well as bridging the skills gap for new workers.
Likewise, manufacturers face an ongoing push to engage in digital transformation to achieve true smart manufacturing capabilities. Each organization’s transformation journey is different and requires a careful evaluation of current digital maturity levels and practical roadmaps for adoption. In today’s fast-evolving market, integrating advanced workforce management strategies is not just a competitive edge but a necessity.
The recent WorkForce Software webinar, Supporting the Move to Smart Manufacturing with Workforce Management Technology, hosted in collaboration with Effective People, showed how the right workforce management strategy can accelerate movement toward smart manufacturing capabilities.
We’ll share some of the insights from the webinar and demonstrate why modern workforce management solutions are pivotal in steering your manufacturing processes towards this new era of technological sophistication and operational excellence.
Smart Manufacturing Brings a New Era of Efficiency and Flexibility
Smart manufacturing is a broad category of manufacturing that essentially uses technology to improve the efficiency, flexibility, and sustainability of the entire manufacturing process. At its core, smart manufacturing leverages digital tools to create interconnected systems that revolutionize the manufacturing process. It offers manufacturers the ability to make smarter decisions in an agile mode, improving production quality, and enhancing operational efficiency.
Some of the high-level key characteristics of smart manufacturing in general are:
- Connectivity: Highly interconnected systems that collect and exchange data are used to optimize the production process and make better decisions. These are often powered by Internet of Things (IoT) sensors that leverage cloud solutions to enable visibility throughout the production process.
- Automation: Smart manufacturing systems use a variety of automation technologies, such as robots, machine vision, and artificial intelligence (AI), to perform tasks that were previously done by humans. This frees up human workers to focus on more strategic and creative tasks.
- Data analytics: Smart manufacturing systems use data analytics to identify trends, optimize processes, and improve product quality. At their best, these systems enable forecasting capabilities that inform how sudden changes in production, downtime, or supply chain challenges will impact production processes.
- Collaboration: Smart manufacturing systems enable collaboration between different departments and stakeholders within a company, as well as with suppliers and customers. This collaboration allows for better decision-making and a more efficient production process.
The manufacturing industry is no stranger to challenges such as economic volatility, regulatory complexities, and safety concerns. Smart manufacturing provides a framework to not only withstand these challenges but to thrive using digital capabilities to forecast needs and streamline collaborative solutions.
What is Cloud-based Modern Workforce Management
Cloud-based modern workforce management is a discipline focused on optimizing business performance while also treating workers as a valuable resource. Modern workforce management meets the critical needs of employees through anywhere mobile accessibility, schedule flexibility, and tools that make workers feel heard and valued. By engaging employees and empowering them with technology, manufacturers can become an employer of choice.
These same capabilities support critical business goals like maximizing productivity, optimizing labor spend, and improving overall operational effectiveness. Advanced analytics provide real-time insights to make data-driven decisions about the workforce. Automation and smart scheduling optimize staffing levels and alignments.
Cloud-based modern workforce management bridges the gap between desired business outcomes and employee expectations. It does this with a modern approach to managing, enabling, and engaging every employee no matter where and when work happens. Workforce management platforms make this level of optimization and insight possible in today’s manufacturing environment.
How Modern Workforce Management Supports Smart Manufacturing Capabilities
Smart manufacturing in the context of modern workforce management leverages technology, automation, and data insights to create a more productive, efficient, and employee-centric manufacturing environment. This aligns the needs of the workforce with the broader goals of the manufacturing process, ensuring that both the employees and the organization thrive in a rapidly changing industry landscape.
Here are some examples of how modern workforce management supports smart manufacturing capabilities:
- Labor Optimization and Workforce Productivity: Cloud-based solutions facilitate labor optimization and workforce productivity by providing real-time monitoring and adaptive scheduling, skill-based staffing, and efficient payroll processing. The key lies in labor optimization – aligning workforce capabilities with operational demands. By strategically scheduling and deploying employees, manufacturers can achieve significant cost savings and efficiency gains. Labor optimization in manufacturing is not merely about workforce allocation; it’s about extracting maximum value and ensuring compliance with labor laws and regulations.
- Employee Experience: A positive workplace environment is crucial. Emphasizing factors such as work-life balance, user experience, ergonomic work settings, and opportunities for growth can significantly boost employee morale and productivity.
- Technological Integration: The integration of technologies like AI, IoT, and intelligent automation can exponentially enhance productivity. These technologies, when effectively implemented, transform the manufacturing landscape, enabling companies to stay ahead of the competition.
- The Critical Role of Communication and Collaboration: Manufacturing processes often involve multiple departments and complex workflows. Effective communication and collaboration are pivotal in ensuring productivity and innovation, especially in large or dispersed teams.
- Compliance and Risk Management: With the complexity of current regulations, intelligent workforce management tools are essential for ensuring compliance, reducing legal risks, and maintaining a safe working environment.
Manufacturing Focused Modern Workforce Management Use Cases
Implementing a modern, cloud-based workforce management system provides manufacturers with a wealth of capabilities to optimize operations, empower employees, and drive smarter decision-making.
Here are a few examples of manufacturing focused use cases:
- Self-Service Portals/Mobile Accessibility: The system can provide employees with self-service portals where they can access their schedules, request time off, view their calculated time, and update their calendar and leave time. This empowers employees to manage their work-related tasks conveniently. Offering a mobile-friendly interface allows employees to access work-related information and perform tasks from their smartphones or tablets. This flexibility enhances convenience and accessibility.
- Flexible Scheduling: Modern systems can offer flexible scheduling options, such as shift swapping and bid-based scheduling, which give employees more control over their work hours. This flexibility can lead to improved work-life balance and job satisfaction.
- Transparent Communication: The system can facilitate transparent communication between management and employees by providing a platform for announcements, updates, and notifications. This ensures that employees are well-informed about company news and changes.
- Work-Life Balance: The system can help monitor employee work hours to ensure compliance with labor laws and policies regarding overtime and work-life balance. This safeguards employees’ well-being.
- Payroll Transparency: Providing clear and detailed pay stubs through the system helps employees understand their compensation and deductions, reducing confusion and enhancing trust.
- Leave and Time-Off Management: The system simplifies the process of requesting and approving time off. Automated workflows ensure timely responses, and clear leave policies contribute to employee satisfaction.
As manufacturers continue embracing smart technologies, optimizing workforce management should be a top priority. A modern cloud-based system creates the workforce visibility, collaboration, and flexibility needed to realize the full benefits of smart manufacturing. By taking a data-driven approach to balancing labor costs and production demands, manufacturers can maximize workforce productivity. Real-time analytics provide the visibility to enhance decision-making and collaboration. And an emphasis on the employee experience helps engage frontline workers driving digital adoption.
Modern workforce management solutions unite critical components: insight, automation, compliance protection, and an empowered workforce. With smart manufacturing on the rise, manufacturers should view optimized workforce management as mission critical. The path forward is clear—invest in cloud-based workforce management to enable the smart factory of the future.
Watch our On-Demand Webinar, Mastering the Future of Manufacturing, to see how modern workforce management can help your organization realize value by unlocking the power of your workforce.
Subscribe to The WorkForce Blog
Learn the art and science of maintaining productive, happy, engaged employees.
Discover More
Nucleus Insights from WorkForce Customers Research Note
Nucleus Research interviews WorkForce customers who validate why we’re ranked the #1 WFM enterprise vendor for 10 consecutive years.
Elevate Employee Experience: Checklist for Operational Leaders
Get the practical steps and technology functionalities operation leaders need to improve their employees’ work experiences.
Streamlining Complex Workforce Compliance Requirements Boosts Productivity
Discover how workforce compliance software helps EMEA organisations navigate complex legislation, enhance compliance and boost operational efficiency.